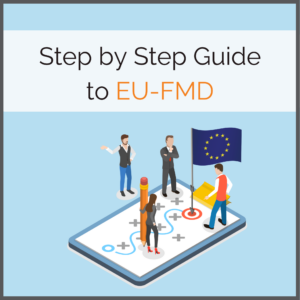
The European Falsified Medicines Directive (EU FMD) came into force on February 9, 2019. For many pharmaceutical companies, this was the first step towards serialization and often required a rapid introduction of digital processes. The situation was different in Italy, Greece, and Belgium. Systems for verifying and tracing medicinal products have been in place here for some time.
As with any major project involving many stakeholders, success is determined by everyone being prepared and doing their part. What challenges did companies face at the time? What did everyone involved learn from these experiences? And what measures can companies in Italy, Greece, and Belgium take today to prepare for the EU FMD?
Historical review: The introduction of the EU FMD
It’s five to twelve. The introduction of the EU FMD is approaching, and the requirements are articulate. From February 9, 2019, pharmaceutical packaging in Europe must have three critical safety features: an anti-tampering device, a 2D data matrix with a unique identifier, a so-called serial number, and an EU Hub report for later verification of the drug package in the pharmacy. Despite the approaching deadline, only a few manufacturers are connected to the EU Hub or have started with the necessary technical, personnel, and financial preparations. That is where tracekey comes into play.
Tracekey is an agile software start-up from Bochum. It is familiar with the requirements of the EU FMD and has recognized that a one-size-fits-all technological solution does not work for small and medium-sized enterprises (SMEs). In a joint project with customers, mytracekey Pharma was created – a scalable cloud solution that is flexibly adaptable, can generate serial numbers, and provides interfaces to other serialization levels.
Looking back, Daniel Althoff, COO at tracekey solutions, describes the situation: “With the introduction of the EU FMD, it became clear that many companies were overwhelmed by the many requirements.” Today, things look very different. Except for a few companies in Italy, Greece, and Belgium, all pharmaceutical companies in Europe are connected to the EU Hub. Company processes are well established, and fulfillment of the EU FMD is virtually a matter of course.
Challenges and experiences
“At the time, there were no best practices or proper tools for dealing with serialization,” says Daniel Althoff, COO at tracekey solutions. What was new for many customers was not only the digital networking with business partners and authorities but also the fact that previously independent departments had to harmonize their processes. Accompanied by tracekey project managers, they jointly outlined when and where batches of medicines are labeled with serial numbers, who reports them to the EU Hub, and what happens in the event of a product recall. It quickly became clear to everyone involved that the acquisition of a new production line for printing the 2D data matrix on the pharmaceutical packaging alone was not enough. Serialization is much more about enabling the exchange of internal and external data.
As a level 4/5 provider of serialization systems, tracekey enables, for example, to centrally manage production data during the serialization process and exchange it with external parties such as contract manufacturers and government systems. Daniel Althoff, COO at tracekey solutions: “Serialisation is not an issue that a company can solve on its own. Even if the customer already has experience with serialization in other countries, the introduction of the EU FMD can still be new territory. After all, reporting obligations for drugs do not exist everywhere.”
Serialization is a continuous process
The constantly changing framework conditions and the initial dynamics of the EU FMD posed a further challenge for many customers. For example, after the EU FMD came into force, interfaces for the EU Hub were added and processes for parallel importers were subsequently mapped. Production plans were changed, and business partners came and went. “Serialisation is a continuous process. It is not a one-off project. Therefore, it is worth investing in your resources or outsourcing projects,” explains Daniel Althoff, COO at tracekey solutions.
To react flexibly to customer requirements and regulatory changes, tracekey works agile. New software updates are installed via the cloud in a regular release cycle and we are always providing our customers with the latest validation documents. That minimizes the workload for all parties. Additionally, thanks to the cloud connection, all customers always benefit from the new features.
EU FMD best practice: What measures to take right now?
From years of working with our customers, we have been able to draw on several experiences and best practices to make a customer fit for the EU FMD or other serialization regulations.
- Early planning: What measures are planned and until when must they be completed? What financial, technical, and human resources are available to you? Do you want to invest in or outsource sub-processes, such as production or serialization management?
- Technical infrastructure: Can your production lines print 2D data matrices? Can you read serial numbers? Do you have suitable software to generate and manage serial numbers and report them to the EU Hub? Are the individual serialization levels coordinated with each other?
- EU Hub connection: Following on from the previous point: Is there a connection to the EU Hub? Is your company already registered with the EMVO?
- Adaptation of company processes: Which departments are involved? Who needs serial numbers, when, and how many? Who creates the labels? Who is responsible for reporting?
- Regulatory know-how: Who will be your serialization expert? Do you know what product data needs to be reported to the EU Hub? How do you keep up to date with regulatory changes?
- Financial planning: Have you factored the costs associated with the EU FMD into your budget? Do you want to invest in internal training or outsource serialization management?
- Business partner connection: Which processes run externally? Which software is used and which interfaces need to be configured?
Start your preparations now and benefit from our experience. Connecting business partners takes time and even registering in EMVO’s OBP portal can take several months.
What can tracekey do for you?
Tracekey has been supporting pharmaceutical companies implementing serialization projects for over ten years. We specialize in solutions and services for small and medium-sized companies. That is because we belong to the SME sector, as do most of our customers. We know what hurdles companies of this size must overcome concerning complex regulatory requirements.
We have an international network of partners, including standardized interfaces to other serialization systems, and can put you in touch with providers of level 2 and 3 solutions if required.
If this sounds interesting to you, please contact us for a discussion or a free product demonstration.